Valve Body and Parts
Casting Suppliers
Valve casting is the base of the manufacturing industry. The valve casting is one of the primary processes through which pipelines, transportation systems, and industry processes supply fluid flow in applications. As the market grows, the right valve body castings suppliers become essential to businesses seeking quality products and solutions. AKP Ferrocast is a trusted supplier of a wide range of castings that fulfill the needs of its global customers. We manage different aspects of valve casting, ranging from materials and production processes to offering unmatched benefits to our valuable clients.
Valve Casting Products
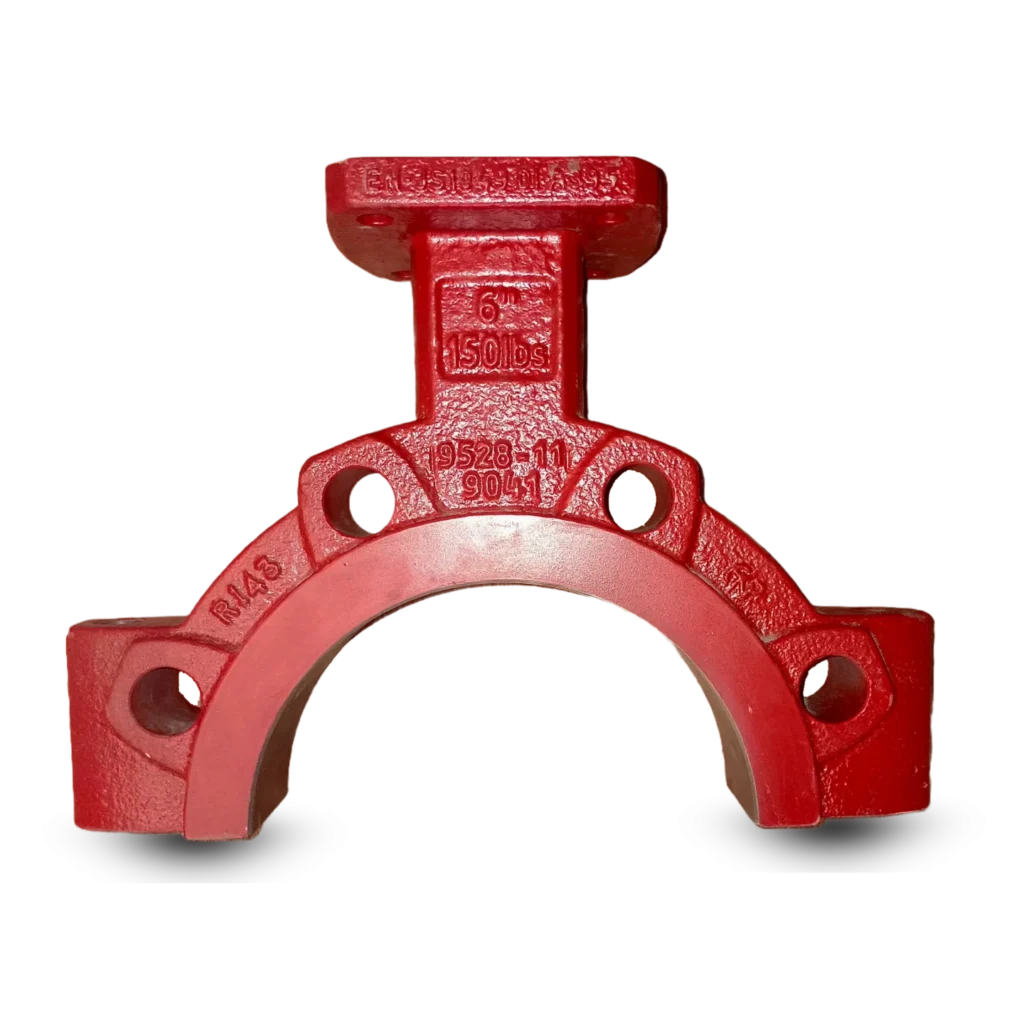
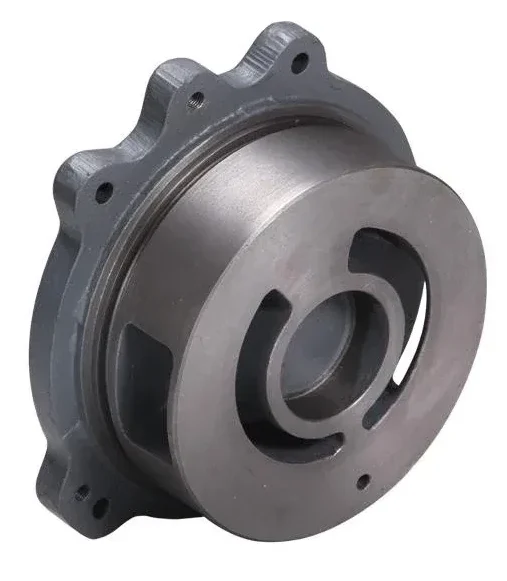
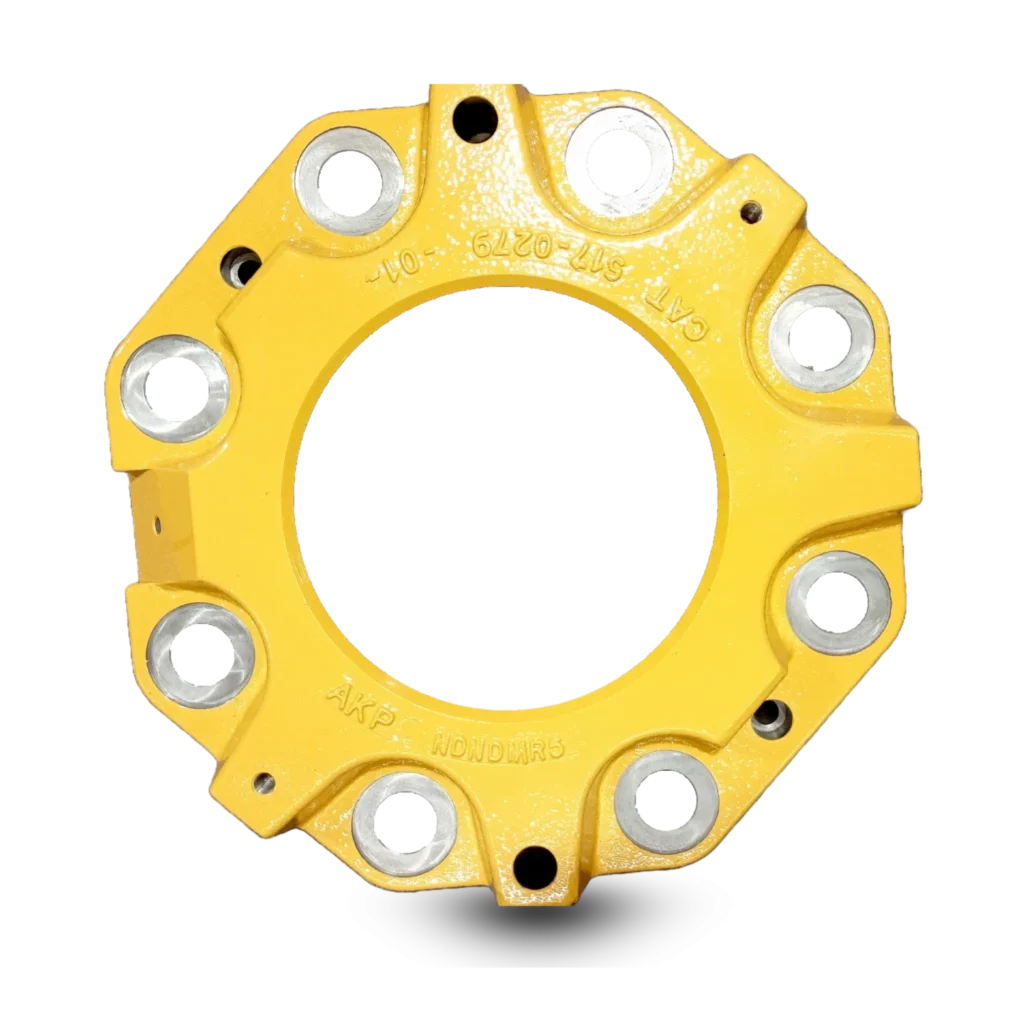
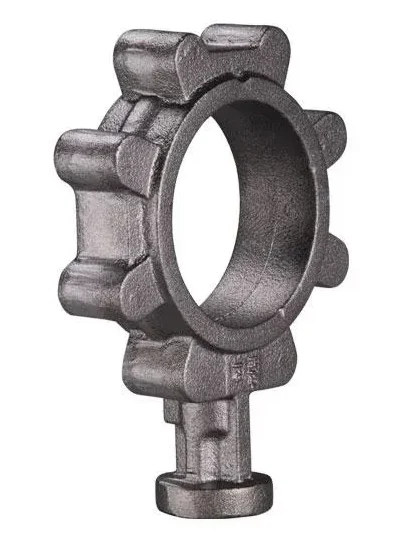
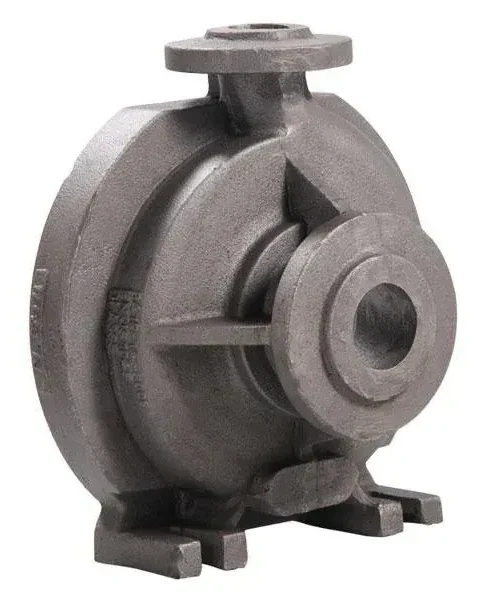
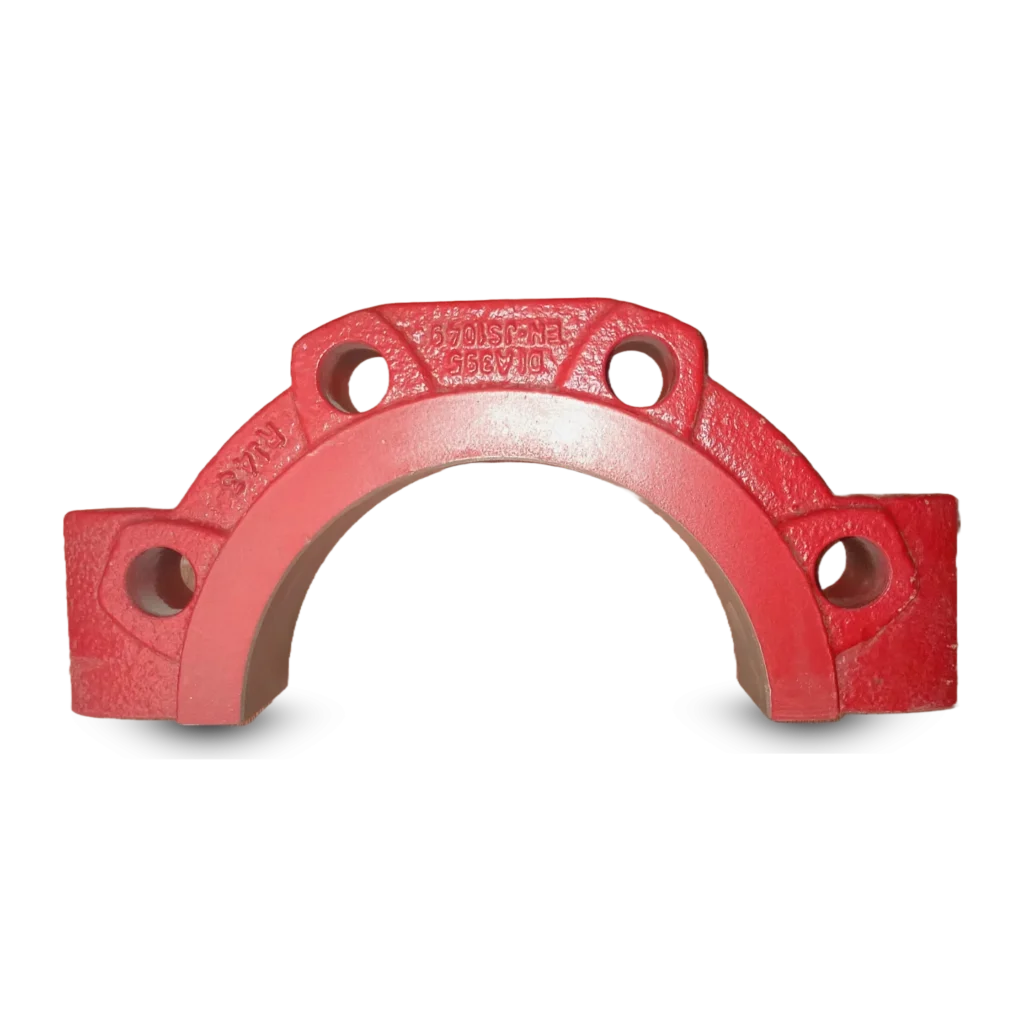
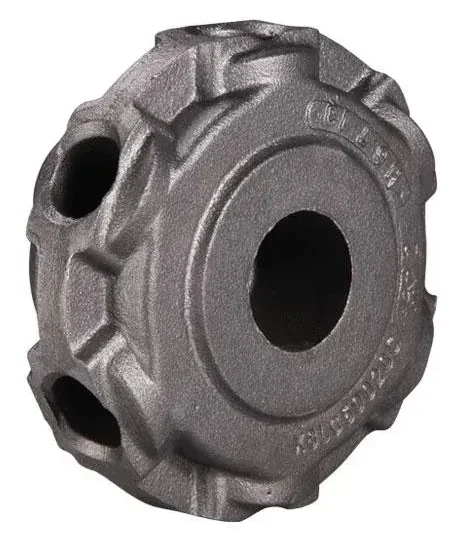
AKP Ferrocast is a leading valve casting manufacturer that offers a wide range of casting valve products designed to answer the different needs of various industries. Our product range includes the following:
- Cast Valve Body: The valve body casting is the main part of a valve where most other parts are housed. This is a part that faces extreme pressure and temperature conditions. We produce cast valve bodies in cast iron and stainless steel with exceptionally accurate dimensions.
- Cast Valve Disc: The disc is the part that controls flow through opening, closing, or partial obstruction of pathways. Our cast valve discs ensure smooth operation and optimum performance of control and cast iron check valves.
- Cast Valve Bonnet: This serves as a valve body casting cover that provides extra sealing against leakage. It is available in various materials and provides strength together with durability.
- Cast Valve Flange: Valve flanges connect the valve to pipes to ensure secure fittings. Our cast valve flanges are available in various sizes and pressure ratings to fit specific industrial needs.
Metals And Grades That We Use for Valve Casting Parts
AKP Ferrocast uses many different metals for valve castings. All are selected for their particular application. Valve castings are produced using both gray and ductile iron based on various international standards. These include gray iron, which has high strength and machinability in accordance with EN-GJL-200, ASTM FG 200, and IS FG 200. Ductile iron with superior strength and flexibility meets requirements according to EN-GJS-400-18, ASTM 60-40-18, and IS SG 400/18. These materials ensure that castings for valve operations provide maximal performance and durability as well as maximal resistance against wear for versatility in industrial use.
Type of Cast Iron (Gray/Ductile)
Gray & Ductile Iron
EN Standards
EN-GJL-200, EN-GJS-400-18
ASTM Standards
60-40-18
IS Standards
FG 200, SG 400/18
Our Commitment
We, at AKP Ferrocast, are dedicated to producing high-quality valve-casting products. Each production stage-from raw material selection to inspection-demonstrates the standard of excellence. Our commitment to investment in innovative technologies and stringent quality control standards ensures that each valve casting meets the best specific industrial standards. This commitment to quality and innovation makes us one of the leading suppliers of valve casting.
Production Process
Our process of casting valve castings involves important steps for precise and quality production.
- Pattern Making: Our process of casting starts with creating accurate patterns or molds for our casting. This process is very critical to exacting the precise dimensions and tolerances.
- Melting: Selected metal is melted at an appropriate temperature. Such a process eliminates the inconsistencies and reduces the occurrence of defects.
- Casting: The molten metal is poured into the molds using sand casting, lost wax casting, or lost foam casting. The technique used depends on the size, material, and application of the product.
- Cooling and Solidification: Once poured, casting is allowed to cool down. The rate at which it cools determines the mechanical properties of the cast metal.
- Finishing and Machining: Once cooled we extract the casting from the mold for finishing operations, including machining for precision, drilling, and surface treatment.
- Inspection and Testing: We conducted a series of tests, such as ultrasonic and magnetic particle testing, to ensure that there were no defects and that the quality of the final product met the standards.
Discover Our Valve Body and Parts Casting Solutions – Elevate Your Manufacturing Process with AKP Ferrocast's Precision Parts.
Our Expertise
AKP Ferrocast has years of experience and is a reputed supplier to the valve casting industry. Our facilities are capable of managing different casting methods and materials to cater to the customised requirements of various industries. We serve various industries, including automobile, agriculture, machinery, and transport industries, with strong and high-quality valve components that comply with strict standards.
Why Choose AKP Ferrocast for Valve Casting?
By choosing AKP Ferrocast as your trusted supplier of valve castings, we offer exceptional benefits such as:
- Wide Range of Materials: We offer a wide variety of materials to serve the different needs of clients for valve components, including cast iron, carbon steel, stainless steel, and ductile iron.
- Advanced Production Techniques: We use advanced techniques like lost wax, lost foam, and sand casting to produce parts with excellent surface finish and high dimensional accuracy.
- Stringent Quality Control: Every single casting undergoes strict quality testing processes involving a non-destructive test to ensure the product meets high-quality levels.
- Global Supply Network: The valve components we manufacture are supplied to global customers, meeting deadlines and on-time deliveries.
Conclusion
At AKP Ferrocast, we produce industrial casting for different industries, such as agriculture, automotive, and machinery, with quality casting in the ever-evolving landscape of industrial manufacturing. Our extensive range of valve components meets quality standards and strictly adheres to advanced manufacturing techniques. We cast ductile and gray casting iron for diversified industries and international valve casting manufacturers with the best casting solutions for their applications.
Frequently Ask Questions
Is a casting valve better than a forging?
Casting is better for complex shapes and intricate designs. Forging provides stronger and more durable results. The choice depends on the application’s requirements and the specific properties the valve will need.
What factors are considered when selecting a valve casting material?
When choosing the right material for casting the valve, consider pressure, temperature, corrosion properties, resistance, environmental challenges, performance, longevity, and the fluid that is controlled.
Which metal is used to make valve components?
Valve components are made from carbon steel, stainless steel, gray cast iron, and ductile cast iron.
What materials are used for valve bodies?
The valve bodies are made out of cast iron, carbon steel, stainless steel, and ductile iron.
Request Pricing Details
Get a comprehensive quote based on your specific needs and requirements. Submit your request to receive detailed pricing, including product specifications, quantities, and delivery terms.